ROC | RETHINKING OF CULTURE
Architectural Association AADRL
Tutor: Theodore Spyropoulos
Year: 2017 - 2018
Introduction
The prototype design methodology is based on the understanding of the vertices defining geometries and joints to support transformability by changing the location of each elements in the system.
The transformative primitive, as basis, which is derived from the potentials of triangle’s being common part of each and every geometry and adapt the same principle to very cube form to alter its geometric definition and space dimension it defines.
Subdivision strategies in that manner is occurred in the way of evaluating and reaching varied geometry then its own itself and spatial deformations by behaviour of joints in the system. While altering the joints of the prototype, the freedom of 360 degree transformation of vertices defining geometry has been put forward is to bring both the limitless geometric mutations and undefinable spatial outcomes.
Hence, the prototype as a first research stage has focused on one way axial transfiguration to change cube to various form of rectangular prism and in-between space as diamond-form prisms.
After experimentations, tests and evaluations through various-scaled prototype and digital animations, final prototype which is controlled by engines, specifically-designed-part with magnets and spheres to promote mobility in the system is to be explained in this very workshop explaining the methodologies of subdivision, transformation, and mobility and diverse states of their combined cartographies.
Triangle/square
“In order to change an existing paradigm, you do not struggle to try and change the problematic model. You create a new model and make the old one obsolete.” 1
R. Buckminster Fuller
To reach the core potential of each and every geometry, the common line of each one is to be researched. The triangle of the universe may be adaptable to any shape by transforming the angular relationship of its lines, i.e. the angles between lines. To be able to control the core triangle of any geometry, the edge of one triangle assumed as spectral one so the other two lines can change their location and relation without any possible restriction one of which is the length of the bottom line.
To utilize the potential of that spectral line, an imaginary line is to be taken as a reference/mirror line for a real triangle. As a final result, the square is considered as the ultimate shape by reflecting triangle based on the mirror line. To do so, by changing joints of two different world -real and spectral-, the square is aimed to be the main transformative shape of many a geometry.
Cube Authority
“Throughout his work the joint is treated as a condensation; as an intersection embodying the whole in part, irrespective of whether the connection in question is an articulation or a bearing or even an altogether larger linking component such as a stair or a bridge.”
Kenneth Frampton analysed work of Carlo Scarpa
Mechanic structures
Approaching the creation of a prototype, it became necessary to look for mechanisms or methods of working with geometry. The required method that would guarantee geometric flexibility, variability and allowing to combine similar objects around. After the research, several mechanical and geometric solutions were found.
The regular grid was used as a basis. In the intersection of lines there were points which became into corners / vertices of parallelepipeds after designing the prototype. The idea was to create control at each vertex to control the geometry of the parallelepiped. The mechanism found could provide very precise control.
The research of joints and their potential behind connections inspired from the level of molecules and atoms from the smallest principles to reach the largest. As in physics, every form is quintessentially to consist of three core components= electrons, neutrons and protons.
The configuration of joints based on the particle relations principles is to be determinant of the transformation directions in the system.
As in the molecular scale ( molecules are able to form gas, liquid, solid), based on the joints connections to each other will enable the simple square / cube to transform into various forms.
Prototype
To reach the multiple subdivision mode of different transformed stage, servo engines are to be introduces to the system as an activator to process subdivision through assigned and recalibrated by different angles embedded in their codes.
Based on the defined subdivided systems, each and every engine is to recognize pre-established angular composition and perform their own matrix to subdivide unit into various volumetric space.
Comparison of different families of the R.O.C. unit showed that most of them don’t have an ability to transform appropriately in the holistic structure, caused by the insufficiency of its geometry.
The transformations, operated by the second and third families do not provide the necessary parametres that are required. According to these studies, the first family, involving only one axis have been taken for further prototype.
Initial researches show that the joints axial movement enable system to have both rigid and soft transformations with diverse quality of spaces. Apart from individual characteristics of each unit, the clustering of transformed spaces offers new type of in-between areas in the system, unexpected anti-voids as space.
Controller
In order to approach the varied kind of subdivided spaces through unit transformation and tested joint systems in earlier models, kinetic control mechanism on appointed control points a.k.a. the joints is the core of the prototype. To do so, servo engines are to be appointed as main part of system of unit to activate subdivision process through transformation rules assigned and recalibrated by different angles embedded in their codes.
Based on the collected data of axial movement behaviour of vertices, in the earlier stage system softness and rigidity are to be controlled by the 8 corners of the proposed frame.
TORQUE test
On this stage of prototype, weight test has been examined to measure the servo engines strength over time to check stability and compatibility for scaled up prototype. Therefore, through the data which are to be collected to evaluate maximum load-bearing capacity of servos, this research is to be used for obtaining the maximum load capacity of servos to update prototype, and analysing how many units can be carried on each ground level unit.
Hence, the servo engine attached part of the frame has been tested to check required information related to weight capacity of engine. Firstly, an empty bowl has been hanged to the end of partial model with a metal wire. Secondly, by adding one object over time the bowl’s weight has been increased to check maximum capacity.
As a result, the system, which has been observed through the whole process, is to be analysed time-based-response to increased weight over time. While the load is to be increased, the speed of transformation slows down. Furthermore, after a level of load introduced to the system, the growing oscillation is to be observed in hanged system of bowl which is the external piece presented to the system.
First test
There is hope in this life I believe we can stand
This is the first successful test for our prototype mk9. We reached the primary target, and now we are going further.
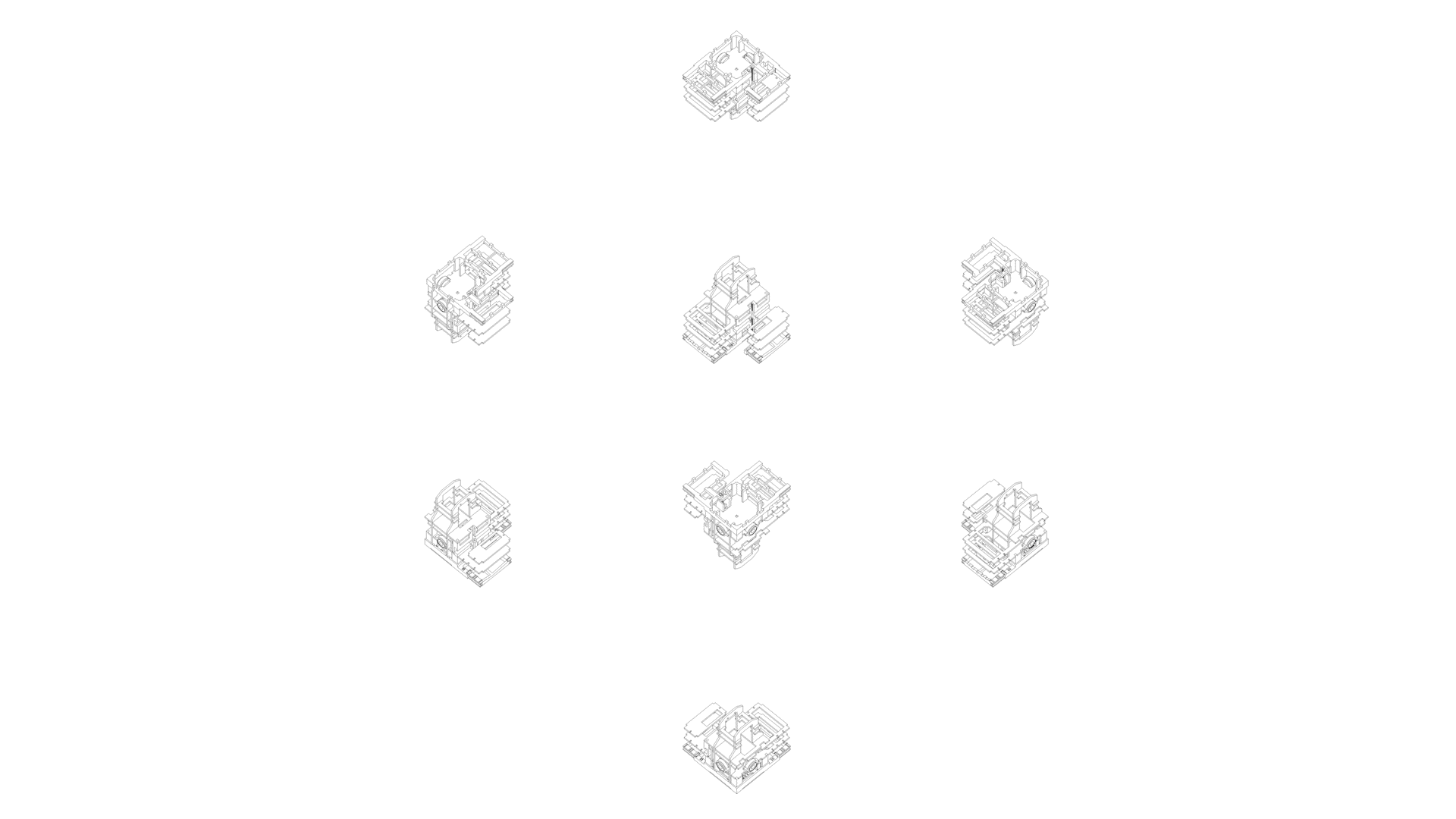
Make it stand out.
Prototype mobility
The prototype and its below frame which has exclusively-designed-mobile part has been tested in every stage to check speed, acceleration and mass response in time. So as to gain spherical rotation in the unit with designed-mechanism, the magnets, sphere-type-wheel and engines, which are to control the directionality of wheels, are to be assembled together. Controlled directionality of the system by engines allows the prototype to be mobile in multiple direction to search other members of its population, reach its target in both architectural and urban scale, and to provide axial transformation in the system.
Multiple unit operations
As a proof of concept prototype have been designed to be mobile, subdivided internal to itself and at the same time interactive with its neighbors. According to this, two units can operate together as well as the single one. With the ability to collapse or subdivide together in certain positions, one unit can also move to or from another one in order to provide enough space for subdivision figure. First one of the prototypes need to reach exact destination and then both of them make a synchronic collapse together. The system can also work vice-verse, when they return to original state and can separate and move from each other.
The system of racks on the top of the protoype provide the ability to slide on another one. So the the whole cluster of units dan reconfigurate within itself.